10
2024
/
07
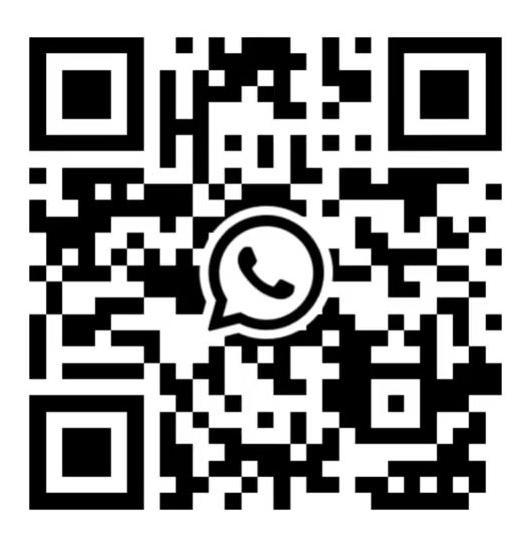
Scan the QR code
Contact us
Email:service@winwinwaterjet.com
Address:63-32 Qixing Street, Shenbei New District, Shenyang City, Liaoning Province
10
2024
/
07
Scan the QR code
Contact us
Email:service@winwinwaterjet.com
Address:63-32 Qixing Street, Shenbei New District, Shenyang City, Liaoning Province